Multi-Echelon Inventory Optimization
Optimize stock across your entire supply chain, reduce costs, and boost service levels. Discover how Multi-Echelon Inventory Optimization (MEIO) transforms supply chain efficiency for a competitive edge.
Going Beyond Traditional Inventory: The Power of Multi-Echelon Optimization
Multi-Echelon Inventory Optimization is a sophisticated strategy that aims to optimize inventory levels across the entire supply chain network. Unlike traditional inventory optimization, which often focuses on individual locations or stages, MEIO takes a holistic approach, considering the interconnectedness of various echelons or levels within the supply chain.
Determining the optimal locations for inventory within the supply chain to balance costs and service levels.
Using advanced forecasting techniques to accurately predict demand at each echelon.
Allocating inventory across different locations based on demand and supply constraints.
Coordinating transportation between echelons to minimize costs and ensure timely delivery.
Why Companies Need MEIO
Complex Supply Chains
Companies with extensive supply chains need MEIO to manage inventory across multiple locations and echelons (levels). This complexity can lead to overstocking or stockouts if not managed properly. MEIO helps streamline inventory across all locations by considering the interdependencies between different parts of the supply chain.
Demand Variability and Lead Times
In retail, consumer demand is often unpredictable, and lead times for replenishing stock can vary across different locations. MEIO optimizes safety stock and replenishment strategies by factoring in variability in demand and lead times, ensuring that stock is available when and where it’s needed most.
Cost Management
By optimizing inventory placement and minimizing stock levels across the supply chain, MEIO reduces carrying costs (such as storage and obsolescence) and transportation costs (e.g., fewer emergency shipments due to stockouts).
Customer Expectations
With rising consumer expectations for faster deliveries and product availability across multiple channels (e.g., e-commerce, in-store), MEIO ensures that companies can meet these expectations without holding excessive inventory.
Unlock Tangible Benefits with MEIO
Lower Inventory Levels
MEIO enables companies to reduce overall inventory without compromising service levels. By optimizing inventory placement and using predictive analytics, companies can operate with less stock while still meeting demand.
Improved Service Levels
MEIO ensures that inventory is available at the right place and time, resulting in fewer stockouts and better on-shelf availability, improving customer satisfaction and loyalty.
Cost Savings
Companies can expect lower carrying costs (storage, insurance, depreciation), reduced transportation costs through more efficient replenishment strategies, and fewer last-minute expedited shipping expenses.
Better Demand Fulfillment
MEIO improves the accuracy of inventory positioning based on demand forecasts, ensuring that stock is in the right place to meet regional and local needs. This helps reduce stockouts and lost sales opportunities, especially in high-demand regions or stores.
Increased Profit Margins
By reducing inventory costs and improving customer service, MEIO can lead to better profit margins through efficient use of working capital and higher sales volumes.
Greater Supply Chain Agility
MEIO enhances a company’s ability to adapt to demand fluctuations and supply chain disruptions. With real-time data visibility and optimized replenishment strategies, companies can react faster to changes in demand or supply chain disruptions, such as natural disasters or global supply issues.
Incorporating MEIO helps retailers and other companies manage the complexities of modern supply chains, reduce operational costs, and improve their service levels to meet customer demands.
Unified Supply Chain Planning
This is not just an evolution in supply chain planning—it’s a revolution.
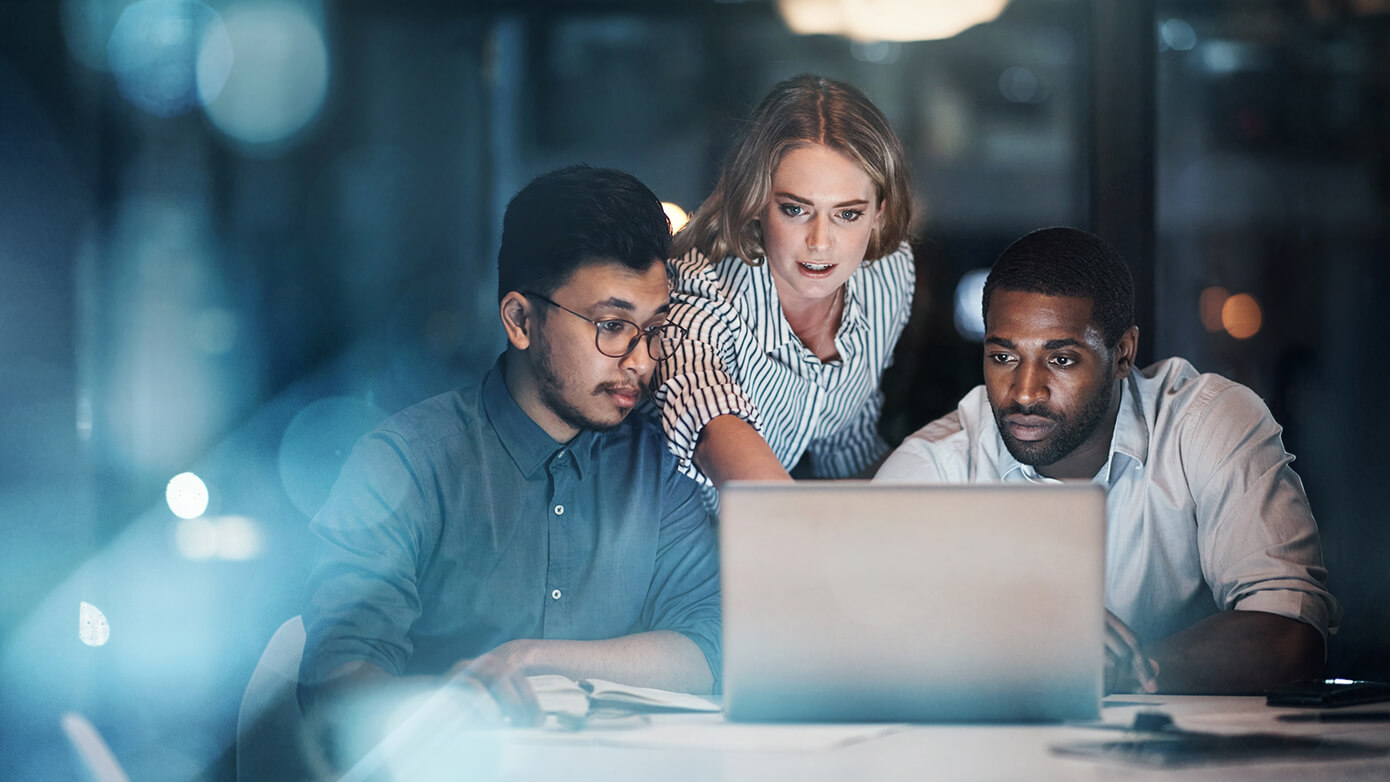
Demand Forecasting
A hybrid approach to forecasting that seamlessly blends the power of proven statistical models with cutting-edge AI.
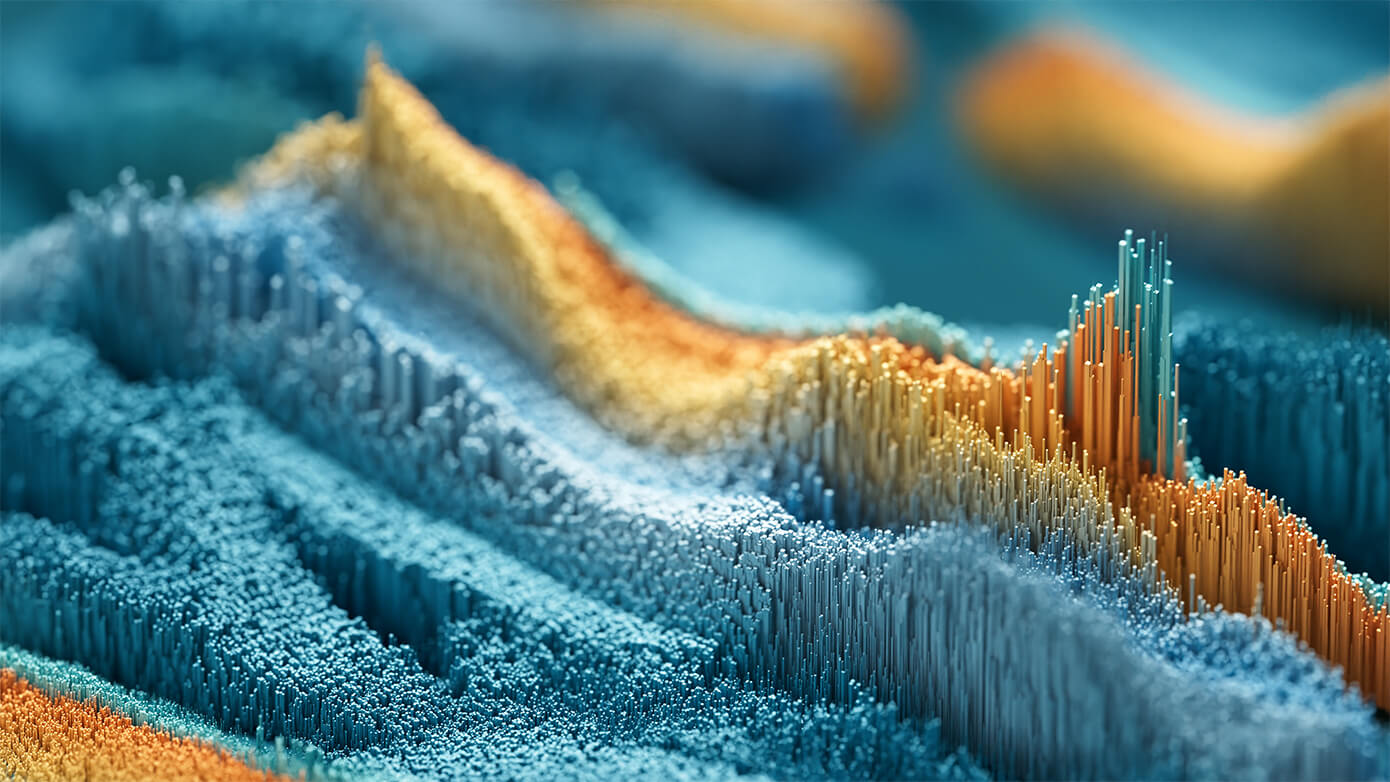
Replenishment
Seamlessly integrates AI-driven insights with real-time data to autonomously optimize inventory levels across all channels, ensuring the right products are always in the right place at the right time, without the need for manual intervention.
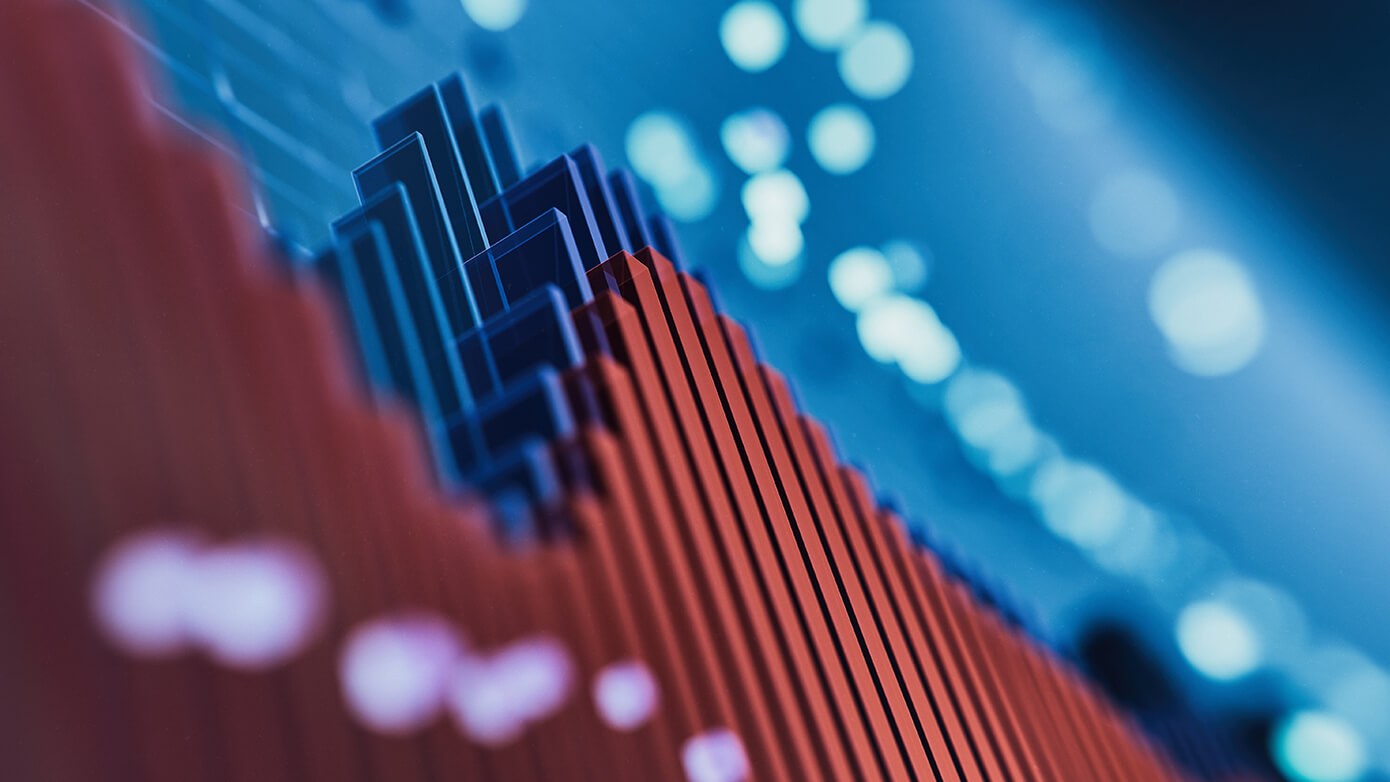
Allocation
Maximize sales opportunities, minimize stockouts, and optimize inventory across all locations and channels with unparalleled precision. Powered by cutting-edge AI and machine learning, our solution ensures your products are always in the right place at the right time.