Carefully Manage Inventory Receiving and Transfers
Get timely and precise handling of inbound replenishment receiving and outbound inventory transfers to improve store inventory accuracy with Manhattan Active® Store Inventory & Fulfillment.
Talk to an Expert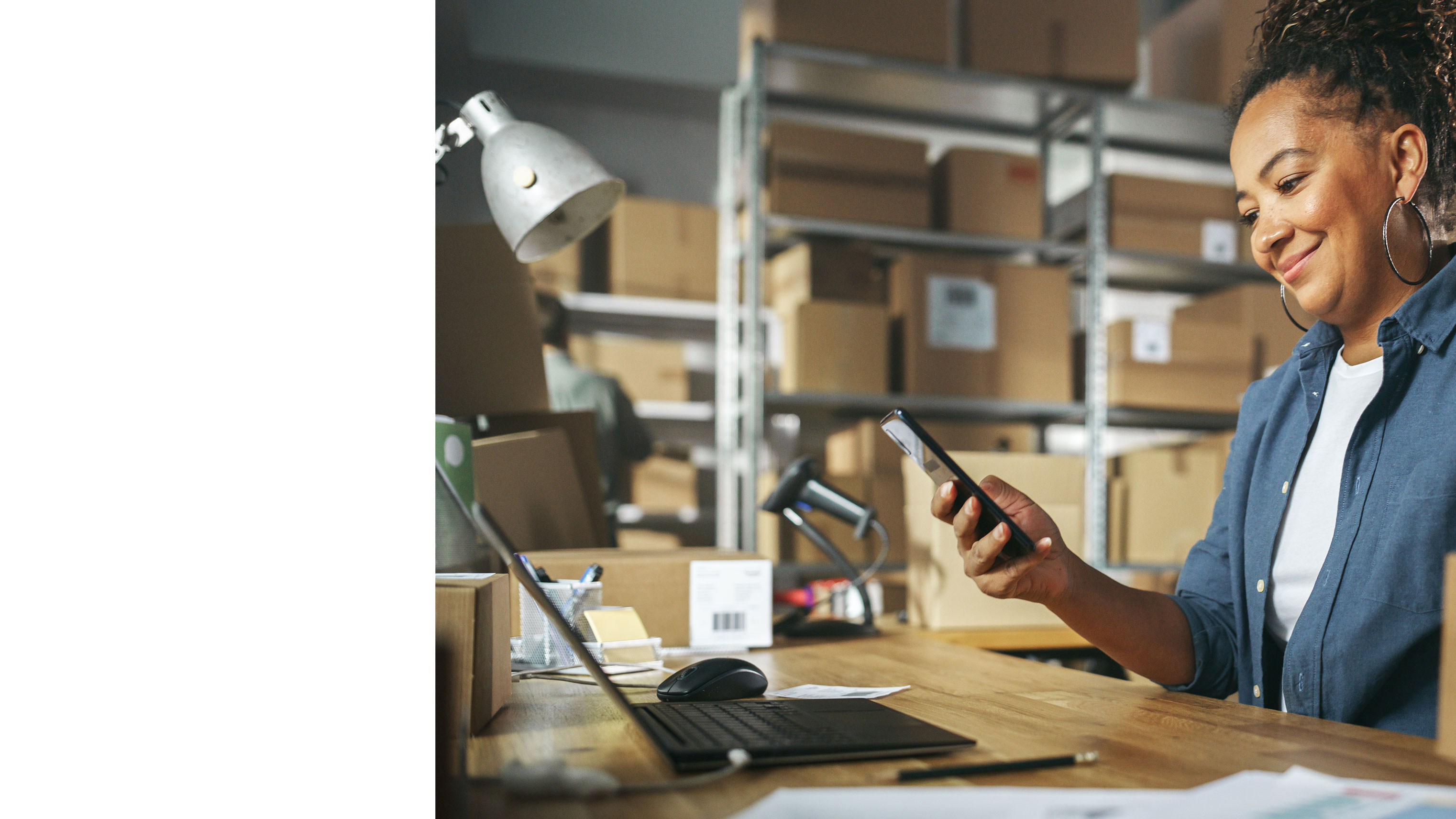
Make Store Inventory Highly Reliable
Store Inventory & Fulfillment
A critical contributor to accurate story inventory is carefully managing the flow of inbound and outbound inventory. Timely and precise handling of these flows is essential to keeping inventory availability data accurate. Manhattan Active Store Inventory strengthens both inbound retail replenishment receiving processes and outbound inventory transfers for improved store inventory accuracy.
Streamlined Retail Replenishment
Manhattan's store inventory management capabilities streamline retail replenishment receiving with the ability to receive store inventory by item, package, case, or load, with support for package level audits, blind receipts, and wrong store receiving. Store associates performing receiving work get detailed guidance about each expected package, including the tracking number, estimated arrival time, carrier, delivery type, origin, and total units in the package. Simplified exception handling for blind receipts, quantity variances, unexpected items, and wrong store alerts associates of anomalies and provides guidance for corrective action.
For example, Manhattan Store Inventory & Fulfillment optimizes receiving blind packages that are unknown from a systems perspective. When a package arrives at the store, but the advanced shipment notice (ASN) is not found in the system, store associates can still scan the contents of the package and update inventory. The blind receiving end-to-end workflow will automatically match the blind receipt to the ASN when it becomes available. This automation simplifies the reconciliation process and ensures these ASNs are not tracked as expected packages in the receiving user interface.
Configurable Receiving Logic and Workflow
Dynamic inventory availability allows stores to set ample time to unpack and put away products before they are exposed online, reducing short picks or inaccurate product availability data. New styles for the season are configurable to automatically be exposed online after a specific number of days, ensuring in-store assortment remains at optimal levels. Configurable replenishment receiving logic, workflows, and notifications, designed from decades of store inventory management experience, optimize the receiving process for improved efficiency and accuracy.
For example, store inventory processes are configurable to automatically determine when a store exposes new inventory receipts to selling channels other than the store. This capability allows stores ample time to unpack the products, reducing short picks. In addition, this capability enables retailers to dynamically expose a new season assortment to the e-commerce sales channel and other stores at a configurable amount of time after being received, providing the store exclusivity for selling the latest assortment. Retailers can define delays in exposure for individual stores and groups of stores, as well as for a subset of products.
RFID-Enabled Inventory Receiving
Manhattan's store inventory application automatically applies RFID to read incoming inventory details from RFID tags. RFID expedites the processing of incoming store inventory receipts with unit-level accuracy and validation, allowing stores to add new inventory to store and enterprise inventory views quickly.
The receiving workflow automatically matches new RFID tags read by overhead readers to expected receipts. Matched packages are pre-loaded on the receiving user interface for store associates to review and confirm the receipt. Store associates can use handheld RFID readers to capture tags that the overhead reader did not detect.
The receiving process supports partially tagged packages of items received with and without RFID tags. If the store desires to assign RFID tags to all items in the store, associates can encode 'generic' RFID tags with handheld readers by assigning a tag to an item that arrived or was returned to the store without a tag or whose tag was damaged.
Expedited Front of House Replenishment
Store sales increase when a product is always available on the sales floor. Manhattan Active Store Inventory & Fulfillment focuses on improving inventory availability on the sales floor, enabling stores to track unit-level inventory between the backroom and front of the house and automatically generate inventory replenishment tasks. After defining the target minimum number of units available on the sales floor, the application instructs store associates on the products that require replenishment based on sales transactions and products available in the backroom.
Receiving of Returns in Stores
Manhattan Active Store Inventory & Fulfillment seamlessly supports receiving returns shipped back to the store. The application automatically identifies the package as a return and initiates a return handling. It guides the store associate through a purpose-built process to capture the returned products and their condition before determining the final routing of the return, such as placing the return in-store stock.
Optimized Inventory Transfers
Inventory can flow in and out of stores outside the regular inventory receiving flow or sales process. End-of-season merchandise for return to the distribution center, rebalancing of stock across stores, ad-hoc requests, damaged items, return to vendor, and more must be cared for with precision to ensure high-accuracy inventory data.
Guided workflows assist store teams in processing inventory transfers, which helps maintain accurate inventory. These workflows make handling transfer orders, packing items, and managing tasks easy. The guided execution of inventory transfers reduces the likelihood of errors or delays.
Store associates can also pack store-initiated and corporate transfer orders by reading unit-level RFID tags instead of scanning item barcodes. Packing by RFID tags ensures that every unit is tracked and accounted for, improving overall inventory accuracy.
To reduce short picks and ensure store associates are not searching for products that are physically in the store but packed for transfer, stores can automatically remove packed inventory from selling channel availability. As soon as a product store-initiated transfer is packed, it is reserved for transfer and cannot be sold.
Store Initiated Replenishment Transfers
As store inventory becomes part of the global inventory for sale across channels, store managers need greater flexibility to initiate store replenishment quickly to meet rising inventory demands. Manhattan supports store-initiated transfers for quick response to low inventory situations, enabling stores to be self-sufficient in managing and creating transfer orders.
Key Takeaways
- Guided and configurable inventory receiving reduces receiving time and increases receiving accuracy to improve the overall store inventory accuracy.
- Configurable receiving allows processes to be tailored to each store, ensuring inventory records are updated at the right time to reflect the true inventory status.
- Inventory transfer capabilities carefully manage the outbound flow of inventory and the inbound flow of ad-hoc receiving of inventory to ensure precise updates of inventory data.
- Optimized replenishment processes, such as automated backroom to sales floor replenishment requests, help keep sales floors stocked, improving sales.
- RFID-enabled receiving, replenishment, and transfers significantly improve efficiency and inventory accuracy.
Related Insights
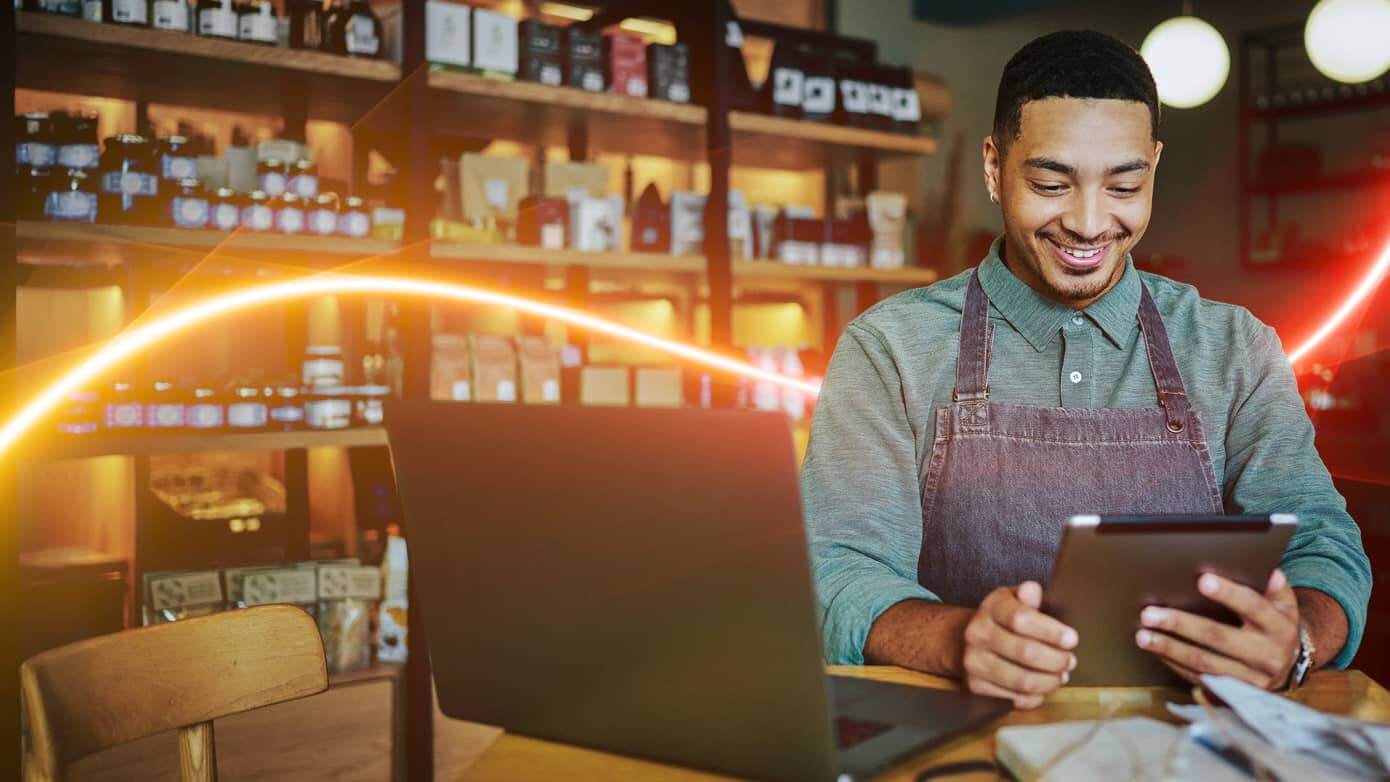
Manhattan Ranks Highest for Store Pick, Pack, and Ship
Read how research and advisory firm Forrester ranked Manhattan the highest for store pick, pack, and ship in the The Forrester Wave™: Order Management Systems (OMS), Q2 2023 report.
Unified Commerce Benchmark for Specialty Retail
See where industry peers stand in offering a consistent and seamless omnichannel experience.
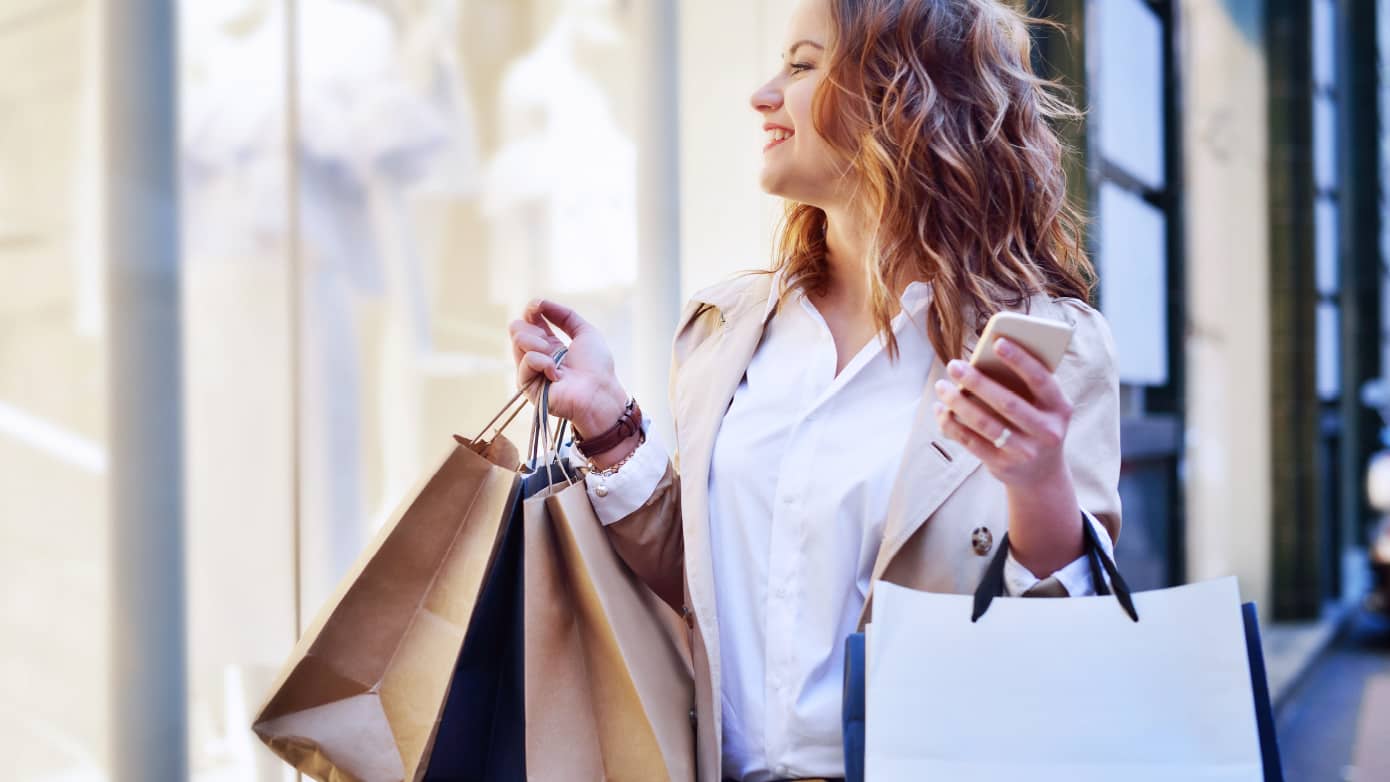
Omnichannel Store Solutions
Discover more about how Manhattan’s store solutions elevate the store shopping experience.
Make store inventory and fulfillment a differentiating part of your omnichannel experience
Learn how Manhattan Active Store Inventory & Fulfillment boosts sales, lowers costs, and improves customer satisfaction by using stores and store inventory to reliably fulfill customer orders.