Mercury Fuels Omnichannel Growth With Manhattan
Customer success story on how Mercury—a leading domestic textile company in China—rebuilt its distribution center to speed up its circulation of products and information while, as a result, also improving its overall execution in inventory, labor, and space with Manhattan’s warehouse management system.
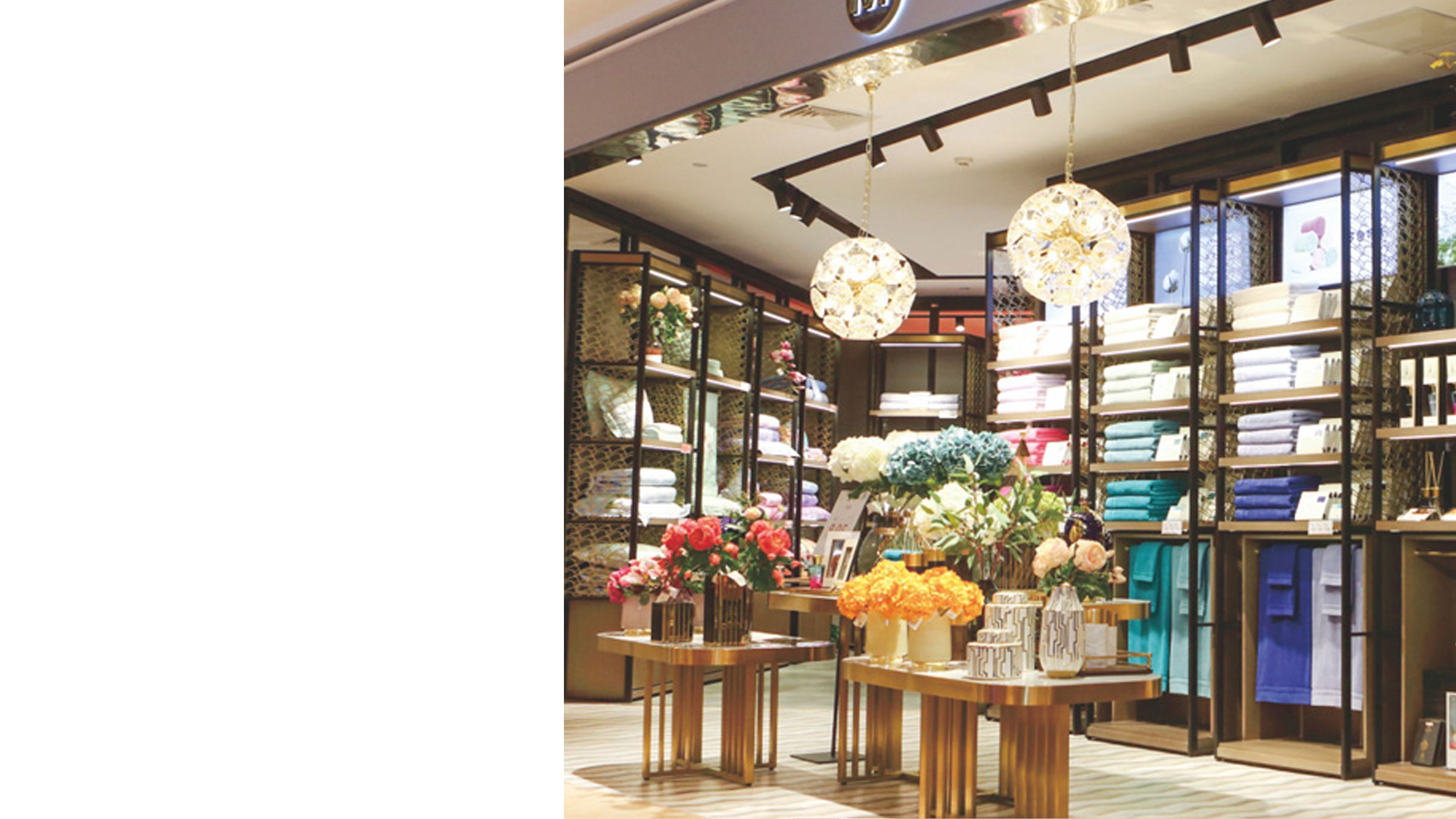
The Challenge
Booming ecommerce demand was driving up Mercury’s orders rapidly, resulting in the need for a comprehensive upgrade of automation, as well as a more streamlined process and better data management.
Operations
Distribution Center: 1 DC (50,000 m2)
Located in Shanghai, China, and serves more than 2,600 specialty stores in China and hundreds of global joint venture stores.
Solution Implemented
Mercury and Manhattan worked together to construct an intelligent logistics distribution center that will leverage highly efficient automation and precision. The goals are better response times and enhanced shopping experiences.
Warehouse Management
Control demand, supply, labor, and automation across your entire network with Manhattan Active® Warehouse Management. The leading cloud-native, evergreen, and extensible WMS in the industry.
Learn MoreProgress & Results
With Manhattan's WMS, the inventory error rate has dropped from 0.05% to 0.003%, the returns can be confirmed by the warehouse within 48 hours, shipping time has shortened from two days to the next day, and inspection capacity has increased from 3,000 pieces/day to 6,000 pieces/day.
Want to Learn More?
Read more about Mercury's new operational efficiency, improved customer experience, and how on China's "Single's Day" Manhattan’s WMS reduced the time it previously spent to fulfill ecommerce orders by four days.